Introduction
Temporary works design is often perceived as the poor relation when compared to permanent works design due to the fact that little or no evidence of its presence remains in the completed project. However, well designed and of course well executed temporary works solutions, can lead to significant cost savings whilst providing a safe and efficient environment for the permanent works to be built. This is particularly the case with below ground temporary works where there are a great many challenges to be faced by a temporary works designer, who is often working right at the end “of the food chain” of information flow. Soil mechanics, whether it is for a shallow trench or a deep basement, is an inexact science at best, relying heavily on engineering judgment to provide a safe, economic and practical solution
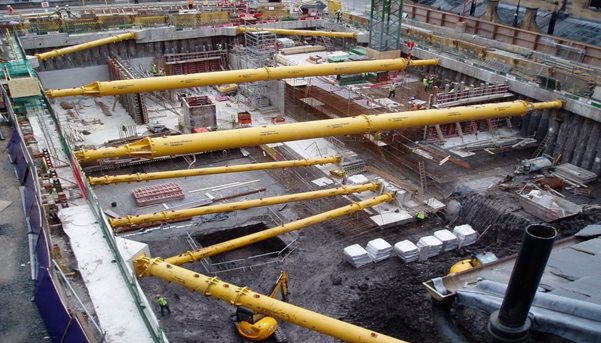
Figure 1 – Temporary propping of deep excavation using modular hydraulic struts
Nowadays the majority of below ground temporary works support is undertaken using proprietary equipment, supplied on a rental basis. Over the last 30 years, the scope of proprietary equipment has increased dramatically. In the 1980’s proprietary equipment was limited to shoring up pipe trenches and small scale pits, which were supported with hydraulically operated aluminum waler frames or Manhole Brace. Today there is a huge range of equipment available to support all sizes of trench, shaft and cofferdam and it is not uncommon to see modular hydraulic struts clear spanning over 50m.
Technical challenges
As the size and complexity of proprietary systems increases, so do the design challenges faced by supply chain temporary works engineers when specifying these systems. Theirs is a constant dilemma; first and foremost, structural adequacy and safety is paramount, which put simply, is the task of balancing forces and resistances whilst leaving a margin for safety. However, the supply chain mantra of no win, no revenue, dictates a need for commercial acceptance. Over-designing and incorporating large, comforting factors of safety is not really an option for “commercial” designers operating in a cut-throat, highly competitive industry.
The introduction of the structural Eurocodes, which are now mandatory on capital schemes, has added more complexity to the design process. Temporary works engineers have generally been reluctant to adapt to the limit state processes, particularly in relation to Eurocode 7 (Geotechnical Design), with it being a radically different approach to previous “working load” methodology. This is certainly the case in relation to smaller scale excavation support, where Eurocode design is considered in the same regard that a sledge hammer is to crack a nut. Indeed, latest BSI published documentation such as PAS 8112 (Guide to the application of European standards in temporary design) continues to refer to “Safe Working Load” non-limit state methodology.
So for the foreseeable future at least, it remains current practice for anything other than a major project, to be designed in accordance with “safe working” or allowable load methodology; equating un-factored calculated loads, based on moderately conservative ground parameters, to allowable or “safe” factored resistances that incorporate a “lumped” factor of safety. Working values for equipment quoted in supplier’s load data charts, tend to be determined by reducing ultimate resistance values by a single factor, typically between 1.5 and 2 for temporary works equipment.
Thermal load considerations when designing long span props
Loading induced by ambient temperature fluctuations can have a large effect on the load in long props and can represent a significant proportion of the design loading. It is essential that thermal loading is considered in combination with the other loads likely to be imposed on a prop see fig 2 below.
Figure 2 - Prop Load diagram
Recent advances in load monitoring technology have enabled the performance of braced excavations to be analysed with a better degree of accuracy and reliability. This information can be of use to engineers in a number of ways such as to compare the predicted and actual performance of support systems and to adopt observational methodology with a greater degree of confidence.
Practical matters
As mentioned earlier, the main advantages with any proprietary system are: availability of equipment; specialist design service; as well as the speed and convenience of installation and removal on site. With shoring systems this is no exception. As the equipment gets bigger though, the installation methodology gets more complicated, particularly on major project type schemes where temporary works is linked more closely with the permanent works construction. Far more detailed planning is required on these projects to avoid costly delays and potential clashes. Larger equipment also puts far more demand on craneage and logistics in general. This has to be scheduled in with the construction of the permanent works.
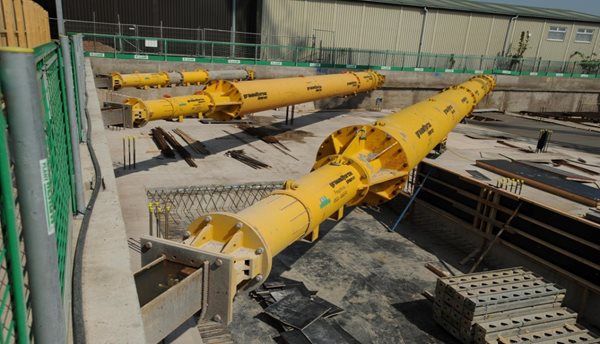
Figure 3 – Integrated connection between prop & RC capping beam
Complex excavation footprints such as shown in Figure 1 will require careful design attention to deal with shear, uplift and lateral forces created by non-perpendicular struts such as knee braces and raking props. Integrated connections as illustrated in Figure 3, cast into capping beams can simplify connection details between the props and the wall, isignificantly, as opposed to relying on bolted shear connections requiring vast amounts of post fixed bolts once the beam has been cast. The former arrangement requires forethought and planning, emphasising the need for early involvement between all parties.
All too often, fundamental decisions on what type of system is to be used and who is supplying it are made at the last minute, which can have significant implications on the success of the project. Connections between struts and capping beams is just one example of how early design cooperation can be of benefit, both in terms of cost and safety.
Summary
To get the best out of proprietary systems, it is essential that the specialist equipment designers get involved in both the permanent and temporary works design process early, as it is often possible, with the vast range of off-the-shelf equipment that is currently available in the market place, to offer innovative solutions, requiring less propping and far greater convenience to the construction process.
Comments
Blog post currently doesn't have any comments.